Получение и исследование морфологии массивов микро- и наностержней ZnO на подложках Si с пленочным подслоем ZnO
Аннотация
Методом карботермического синтеза на подложках кремния с тонкими пленочными подслоями оксида цинка, с использованием меди в качестве катализатора роста получены массивы вертикально ориентированных стержней оксида цинка. Определена оптимальная температура роста этих структур – 770 оС. Установлено, что при температурах на 50 оС выше и ниже данной (820 оС и 720 оС, соответственно) рост стержней подавляется. Показана возможность варьирования средней длины и диаметра стержней путем изменения толщины пленочного подслоя в диапазоне 50 – 100 нм. При толщинах подслоев вне указанного диапазона рост массивов вертикально ориентированных стержней оксида цинка также подавляется.
Ключевые слова: оксид цинка, микро- и наностержни, карботермический метод синтеза, пленочный подслой, катализатор роста.
Введение
Массивы нитевидных нанокристаллов и наностержней ZnO в настоящее время рассматриваются в качестве элементной базы высокоэффективных электрооптических устройств (cветоизлучающих диодов, лазеров и фотодиодов УФ-видимого диапазона, преобразователей солнечной энергии), эмиттеров электронов, сенсоров химических и биологических веществ, микро- и наноэлектромеханических систем (фильтры и генераторы на объемных акустических волнах, датчики вибраций, акселерометры, пьезоэлектрические преобразователи энергии). Значительный интерес также представляет разработка технологии самоорганизованного роста массивов полупроводниковых нитевидных нанокристаллов и гибридных структур на их основе.
В последние два десятилетия разработано множество различных химических и физических методов синтеза полупроводниковых микро- и нанокристаллов, в том числе на основе ZnO. Благодаря простоте технической реализации, группа CVD-методов рассматривается как одна из наиболее перспективных для промышленного получения массивов нанокристаллов ZnO. К данной группе относятся метод карботермического синтеза и метод термического испарения [1-3]. К настоящему времени широко изучены оптические, электрические, структурные свойства наноструктур ZnO, синтезируемых данными методами [4, 5]. Продолжается поиск различных катализаторов роста нитевидных нанокристаллов для возможности варьирования технологии получения и улучшения их оптических и электрических свойств [6-8].
Прикладные характеристики массивов нанокристаллов ZnO определяются не только механическими, оптическими, электрическими и структурными свойствами их отдельных элементов, но так же и свойствами, связанными с морфометрическими параметрами массивов (характерные размеры отдельных элементов, степень дисперсности, плотность и однородность распределения по поверхности). Для многих приложений морфологические характеристики являются определяющими. Актуальной задачей является управление данными параметрами посредством изменения условий синтеза (температуры синтеза и потока вещества, применения различных подслоев и катализаторов роста и т.д.). В данной задаче все еще существует множество нерешенных проблем. Интерес к данному кругу проблем вызван существенной, а зачастую и определяющей ролью интегральных свойств массивов нанокристаллов ZnO в процессах транспорта носителей заряда, поглощения и рассеяния света, чувствительности к химическим веществам, распространения акустических колебаний и т.д.
Кроме этого, при создании устройств на основе массивов ZnO нанокристаллов необходимо производство электрических контактов и/или формирование гетеропереходов на поверхности кристаллов, возможное только посредствам напыления различных материалов. Разработка технологии напыления металла или полупроводникового материала на структуру с развитой поверхностью представляет собой весьма сложную технологическую задачу, требующую большого объема исследовательской и экспериментальной работы. Процессы создания гетеропереходов и электрических контактов во многом будут определяться морфометрическими параметрами исходных массивов нанокристаллов ZnO.
Целью данной работы является изыскание возможностей управления морфометрическими параметрами массивов нано- и микрокристаллов ZnO на подложках Si с пленочным подслоем ZnO в процессе карботермического синтеза с использованием меди в качестве катализатора роста. В задачи входит изучение влияния температуры синтеза и толщины пленочного подслоя на морфометрические параметры нано- и микрокристаллов ZnO: длины и диаметры, степень дисперсности, плотность и однородность распределения по поверхности подложки.
Экспериментальная часть
Получение наностержней ZnO осуществлялось методом карботермического синтеза с использованием подложек Si (100). В качестве катализатора роста применялась медь в виде сверхтонких пленок (эквивалентной толщиной 1 nm) [9]. Синтез наностержней проводился на предварительно нанесенных пленочных подслоях ZnO толщиной 30 – 120 нм. Получение пленок Cu осуществлялось методом магнетронного распыления на постоянном токе при следующих условиях: расстояние мишень-подложка 80 мм, напряжение разряда 150 В, ток разряда 30 мА, давление аргона 1,5×10-3 мм. рт. ст. Получение пленочных подслоев ZnO производилось методом импульсного лазерного напыления. Лазерное излучение KrF-лазера CL-7100 (l = 248 нм, τ = 15 нс) с энергией 300 мДж фокусировалось на поверхность вращающейся мишени с плотностью энергии ~ 2 Дж/см2. Расстояние мишень-подложка составляло 75 мм. Напыление пленок ZnO происходило в атмосфере кислорода при давлении 1,5×10-2 мм. рт. ст. Подложка нагревалась до температуры ~ 500 оС. Толщина покрытий ZnO контролировалась по числу импульсов.
При проведении карботермического синтеза в качестве ростовой камеры использовалась кварцевая труба с внешним резистивным нагревателем. Подложка располагалась в центр нагревателя на расстоянии L = 10 мм от источника испаряемого материала – таблетки ZnO:С в молярном соотношение 1:1. В качестве транспортного газа использовался Ar при давлении 750 мм. рт. ст. и скорости потока 20 см3/мин. Центральная часть печи нагревалась в течении 18, 25 и 35 мин. до рабочих температур 720, 770 и 820 °С соответственно. Время выдержки рабочей температуры составляло 15 мин. Охлаждение рабочей зоны осуществлялось естественным образом до температуры ~ 150 оС, после чего образец вынимался из камеры синтеза.
Морфология полученных образцов изучалась методом сканирующей электронной микроскопии на приборе Zeiss SUPRA 25. Для характеризации морфометрических параметров массивов наностержней выполнялся статистический анализ: с помощью прикладной программы Image Scope по электронно-микроскопическим изображениям определялись диаметры и длины наностержней на поверхности площадью ~ 4 мкм2. Полученные статистические данные визуализировались графически в виде гистограмм распределения по размеру и обрабатывались в программе Origin 7.0.
Результаты
При описании морфологии получаемых структур далее будем пользоваться следующими терминами и положениями. Средняя длина и диаметр стержней – положение максимума функции, используемой для аппроксимации гистограммы распределения по длине и диаметру соответственно. Средняя степень дисперсности – ширина на половине высоты функции, используемой для аппроксимации гистограммы распределения (по длине или диаметру стержней) в единицах размера (нм). При этом, будем говорить, что средняя степень дисперсности по длине соответствует среднему перепаду высоты в образце. Если аппроксимация гистограммы производится двумя кривыми, то за значение ширины результирующей кривой (и, следовательно, средней степени дисперсности) будет приниматься сумма ширин отдельных кривых. Аппроксимация гистограмм распределения по длине производилась функцией Гаусса, а гистограмм распределения по диаметру – функцией логнормального распределения. Под поверхностной плотностью массивов стержней будет пониматься общее количество стержней, приходящихся на единицу площади поверхности.
Исходя из результатов электронно-микроскопических исследований, было установлено, что наиболее интенсивный рост стержней ZnO наблюдался при температуре синтеза 770 оС (рис. 1 b). Снижение температуры до 720 оС и увеличение до 820 оС приводило к подавлению роста стержней. При более низкой температуре синтеза формировались отдельно стоящие кристаллы поперечным сечением ~ 300 нм в плоскости и высотой не более 150 нм (рис. 1 a). Форма таких кристаллов представляла собой призму с неправильным многогранником в основании. При более высокой температуре (820 оС) формировались стержни длиной не более 300 нм и диаметром ~ 100 нм (рис. 1 с) на массивных основаниях неправильной формы Основания стержней срастались друг с другом в плоскости поверхности подложки, имея поперечное сечение ~ 400 нм и высоту ~200 нм.

Рис. 1. Изображения сканирующей электронной микроскопии структур ZnO, полученных при температурах карботермического синтеза 720 оС – a), 770 оС – b) и 820 оС – c) на пленочных подслоях ZnO толщиной 80 нм. Все три изображения выполнены под углом 60 град. к поверхности.
Таким образом, был определен оптимальный диапазон толщин подслоев (50 – 100 нм) и температура синтеза (770 оС) для получения массивов вертикально ориентированных стержней ZnO.
Теперь, перейдем к более детальному описанию массивов вертикальных стержней оксида цинка, полученных при оптимальной температуре синтеза (770 оС) и различных толщинах пленочных подслев ZnO в диапазоне 50 – 100 нм (60 нм, 80нм, 100 нм). При толщине подслоя 60 нм полученные стержни демонстрируют неоднородное распределение по размерам. Как видно из рис. 3 a), в распределении стержней по длинам отчетливо различимы два максимума вблизи значений 800 нм и 1450 нм, причем количество более длинных стержней приблизительно в 2 раза больше. Значение средней дисперсности по длине составляет ~ 1100 нм. Следовательно, и средний перепад высоты в данном образце составляет ~ 1,1 мкм. Подобная картина наблюдается и в распределении по диаметрам, где также можно выделить два максимума при значениях 80 нм и 110 нм с преобладанием более тонких стержней в 2 раза по количеству (рис. 3 b). Значение средней дисперсности по диаметру составляет ~ 80 нм. Поверхностная плотность массива составляет ~ 25 мкм-2.
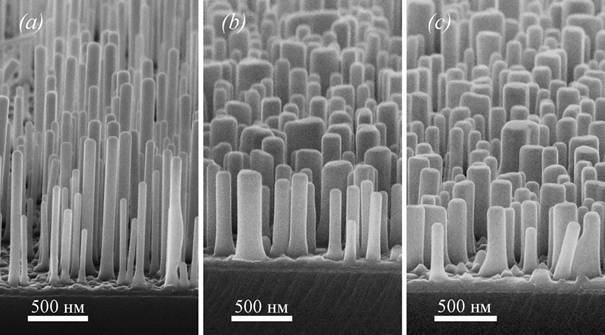
Рис. 2. Изображения сканирующей электронной микроскопии массивов стержней ZnO, полученных при температурах температуре карботермического синтеза 770 оС на пленочных подслоях ZnO толщиной 60 нм – a), 80 нм – b) и 100 нм – c) Все три изображения выполнены под углом 5 град. к поверхности.
Стержни, полученные на подслое ZnO толщиной 100 нм, демонстрируют наиболее однородное по сравнению с двумя предыдущими случаями распределение по длине, хорошо аппроксимируемое одной функцией Гаусса (рис. 3 e). Среднее значение длины составляет 675 нм, а средняя степень дисперсности – 260 нм. Средний перепад высоты лежит на уровне 0,25 мкм. Средний диаметр стержней в данном образце наибольший из всех трех, и составляет 155 нм. Значение средней дисперсности по диаметру здесь также наибольшее – 105 нм (рис. 3 f). Поверхностная плотность массива составляет ~ 18 мкм-2.
Рис. 3. Гистограммы распределения стержней ZnO по длине – a, c, e) и диаметру – b, d, f). Гистограммы представляют распределения по размерам для стержней, полученных с использованием пленочных подслоев ZnO толщиной 60 нм - a, b), 80 нм – c, d) и 100 нм – e, f).
Выводы
Таким образом, методом карботермического синтеза на подложках кремния с тонкими пленочными подслоями оксида цинка, с использованием меди в качестве катализатора роста были получены массивы вертикально ориентированных стержней оксида цинка. Определена оптимальная температура роста данных структур – 770 оС. Установлено, что при температурах на 50 оС выше и ниже оптимальной (820 оС и 720 оС, соответственно) рост стержней подавляется. Показана возможность варьирования средней длины и диаметра стержней путем изменения толщины пленочного подслоя в диапазоне 50 – 100 нм. Установлено, что при возрастании толщины подслоя уменьшается значение средней длины стержней и уменьшается средний перепад высоты массивов (~ 1100, 500 и 250 нм при толщинах подслоев 60, 80 и 100 нм, соответственно), характеризуемый шириной распределения стержней по длине. Значение среднего диаметра стержней возрастает с ростом толщины подслоя (80, 145, 155 нм при значениях толщины подслоев 60, 80 и 100 нм, соответственно). При толщинах подслоев вне диапазона 50 – 100 нм рост массивов вертикально ориентированных стержней оксида цинка также подавляется.
Работа выполнена при финансовой поддержке Минобрнауки, грант ФЦП «Проведение центром коллективного пользования научным оборудованием «Высокие технологии» Южного федерального университета поисковых научно-исследовательских работ в области создания экологически чистых технологий получения новых активных нано- и микроструктурированных материалов для использования в современной сенсорике», госконтракт № 16.552.11.7024.
Литература
[1] H.J. Fan, F. Fleischer, W. Lee, K. Nielsch, R. Scholz, M. Zacharias, U. Gösele, A. Dadgar, and A. Krost // Superlattices and Microstructures. 2004. V. 36. P. 95–105.
[2] Jinhui Song, Xudong Wang, Elisa Riedo, and Zhong L. Wang // J. Phys. Chem B. 2005. V. 109. N. 20.
[3] S.H. Dalal, D.L. Baptista, K.B.K. Teo, R.G. Lacerda, D.A. Jefferson, and W.I. Milne // Nanotechnology. 2006. V. 17. P. 4811–4818.
[4] Jinmin Wang, Lian Gao // J.. 2004. V. 262. P. 290-294.
[5] A. Umar, S.H. Kim, Y.-S. Lee, K.S. Nahm, Y.B. Hahn // J. of Crystal Growth. 2005. V. 282. P. 131-136.
[6] Кайдашев В.Е., Кайдашев Е.М., Peres M., Monteiro T., Correia M.R., Sobolev N.A. // ЖТФ. 2009. Т. 79. В. 11. C. 45–49.
[7] R. T. Rajendra Kumar, E. McGlynn, M. Biswas, R. Saunders,G. Trolliard, B. Soulestin, J.-R. Duclere, J. P. Mosnier, and M. O. Henry // J. Appl. Phys. 2008.V. 104. P. 084309.
[8] Seu Yi Li, Chia Ying Lee, Tseung Yuen Tseng // J. of Crystal Growth. 2003. V. 247. P. 357-362.
[9] Н.В. Лянгузов, В.Е. Кайдашев, Е.М. Кайдашев, К.Г. Абдулвахидов. // Письма в ЖТФ. 2011. Т. 37. В. 5. С. 1-8.